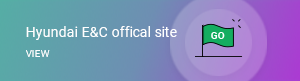
Experience itself is a powerful weapon, especially the experience of someone who has been committed to one specialty. One of the key reasons how Hyundai Engineering and Construction (Hyundai E&C) came to its position on the global stage is because of the people who trained themselves for a long time to become experts in their respective fields. Hyundai E&C writes a special feature based on interviews with in-house experts, who have been at the core of the company’s competitiveness.
[ Oh Seung-joon sitting in front of the camera with a cheerful look. He is a nuclear power expert at Hyundai E&C who has been working at NPP sites in Korea and abroad since 2006. ]
Oh Seung-joon, a nuclear decommissioning manager at Hyundai E&C says
“nuclear business expert Hyundai E&C also excels in nuclear decommissioning!”
No one can deny that Hyundai E&C is a specialist in constructing large nuclear power plants(NPPs). It has led the construction of 24 out of 36 large Korean-type NPPs domestically and internationally, with an unrivaled track record among Korean builders. Hyundai E&C aims to become a ‘Total Solution Provider’ that covers the entire NPP sector. It is expanding its realm of business by venturing not only into small modular reactors (SMR), leading next-generation NPP, but also nuclear decommissioning, also known as the blue ocean in NPP business. As a result, Hyundai E&C will cover the entire scope and lifecycle of nuclear power projects.
Among others, Hyundai E&C's confidence in the field of nuclear decommissioning is particularly strong. As Korea's top builder, it knows the ins and outs of building large NPPs, which gives it a competitive edge in nuclear decommissioning as well. Oh Seung-joon, the Chief Manager of Hyundai E&C's Nuclear Power Division, is a nuclear power specialist who has been working in this field since joining the company in 2006. He has experience working at the Singori NPP Units 1 to 4 and the UAE NPP construction site, and has been involved in a process similar to nuclear decommissioning during the Hanbit Unit 3 and 4 steam generator replacement project. He also contributed to securing the commercialization of nuclear decommissioning site restoration technology. We caught up with Oh Seung-joon, who is currently busy traveling between Korea and the U.S. to manage the Indian Point Nuclear Decommissioning Project in the U.S. and prepare for the deployment of the FOAK (First of a kind) SMR-160* model."
*The SMR-160 is a standard mode or design being detailed by Hyundai E&C in conjunction with US nuclear company Holtec International. It is a 160MW light water reactor that can be deployed in various locations, including deserts and polar regions, without any regional or environmental restrictions. The SMR-160 will be deployed for the first time at the 'Oyster Creek' nuclear decommissioning site owned by Holtec International. The detailed design delivered by Hyundai E&C will not only be used to apply for the first SMR construction permit in the U.S. but also for the design of future SMRs deployed around the world.
Of the 203 permanently shut down reactors, only 21 have been decomissioned
Nuclear power has once again come into the spotlight, with nuclear decommissioning emerging as a new business due to its huge market potential. The world's first NPP began operating in June 1954, and since then, 647 NPPs have been constructed in various countries. According to the International Atomic Energy Agency (IAEA), as of November 2022, more than 65% of the 423 nuclear reactors in operation have reached their design life. Of the 203 reactors permanently shut down, only 21 have been decommissioned. The IAEA predicts that by 2050, a total of 588 reactors will be permanently shut down, representing a market worth a staggering 440 trillion won. However, only four countries in the world have experience in nuclear decommissioning.
“The fact that few countries have decommissioned NPPs compared to the size of the market is good news for us. It means that no one company or country has a technological edge yet. My role is to secure the necessary technology to enable Hyundai E&C to become a leader in the nuclear decommissioning market, which represents a new area of business within the nuclear power generation industry."
Cooling and removal of spent nuclear fuel, decay heat cooling is key
Nuclear decommissioning refers to a series of processes to safely dispose of reactors that have reached the end of their lifespan and return the site to the condition it was in before the plant was built. Largely, it consists of ▶ Permanent shutdown ▶ Spent nuclear fuel removal ▶ Decontamination and demolition ▶ Site restoration. Nuclear decommissioning takes at least 15 years, requiring a high level of process management and technology.
When a NPP is declared permanently shut down, the process of cooling and disposing of the spent nuclear fuel* begins. Just as brewing an espresso leaves behind coffee grounds, operating a NPP inevitably produces spent nuclear fuel. Spent nuclear fuel is a high-level radioactive waste* that emits stronger radiation and higher heat than unspent nuclear fuel, and is stored and managed in a tank-type storage inside the NPP. It is then transferred to an external storage facility and permanently isolated 500 meters below ground.
*Spent nuclear fuel: fuel (uranium, plutonium, etc.) used to generate electricity in NPPs.
*High-level radioactive waste: Radioactive waste with a high radiation intensity.
Radiation - Radioactivity – Radioactive. How do they differ?
·Radiation: A flow of energy, such as particles, light, or waves, emitted by an element in an unstable state as it changes to a stable state.
·Radioactivity: The intensity of radiation, or the ability to give off radiation. ·Radioactive: The property of a substance that contains radioactivity. A substance with the ability to emit radiation is called a ‘radioactive substance’. |
It can take up to five years or more for the temperature and radiation levels of spent nuclear fuel to decrease to a point where it can be safely carried out. During this time, preparations for decommissioning the NPP are made, including planning safety and process controls and carry-out and cost estimates. Once the fuel is cool enough, it is sent to an off-site storage facility. There are two ways to store spent nuclear fuel: wet storage, in which reactor is submerged in water to cool the decay heat*, and dry storage, in which the spent fuel is placed in concrete or metal containers and cooled by air. Most countries choose dry storage because it is more economical and easier to maintain. The core of dry storage is the cask, which is a special shielding container that can withstand strong radiation, high heat, various vibrations, and shocks, and it is essential for NPP decommissioning.
*Decay heat: Radioactive materials continue to decay and give off heat until they turn into stable elements, which is called decay heat. The key to decommissioning a NPP is to cool this decay heat down. Even after a permanent shutdown, reactors reportedly emit as much as 6 to 7 percent of their output during operation. There is currently no way to reduce this decay heat instantaneously. To reduce the high heat, it must be cooled naturally with water or air.
[ An off-site storage facility for spent nuclear fuel at U.S. nuclear company Holtec International; the cylinders, spaced at regular intervals from center to right in the photo, are casks ]
“A cask is a specialized shielding and storing vessel with a complex design. Holtec International is a leading U.S. nuclear company that works with Hyundai E&C. Half of the world's dry storage facilities use Holtec casks. Currently, Hyundai E&C is working on a U.S. nuclear decommissioning site owned by Holtec International, handling construction as well as cask storage and transportation. The project is expected to be a good portfolio for domestic and foreign nuclear decommissioning orders in the future. "
Applied robotics technology to NPP decommissioning... Received Korea's first green certification for radioactive contaminated soil restoration
Once all the spent nuclear fuel has been removed, the next step is to eliminate the radioactive materials of the reactor. This is necessary for the structure to be demolished and the waste to be safely disposed of. Decontamination is the critical process that removes the radioactive material, which is usually done by wiping off the radioactive material with a special liquid or by cleaning and grinding the surface. Since human intervention is need in the process of structure demolition and waste treatment, radioactive materials are removed in two stages.
“Decontamination should be completed before we can get people in the site. In recent years, there has been active adoption of robotics technology in this stage. At Hyundai E&C, we are using our AI robot dog, ‘Spot’, to monitor radiation levels in advance. We believe that the day is not far off when robotics technology will be applied to nuclear decommissioning sites.”
[ Robotic automation is also applied to reactor cutting. ]
The final step in decommissioning a NPP is site restoration, which involves returning the land to its natural state. Hyundai E&C acquired the following technologies for site restoration through the 2019-2021 project on <Evaluation of Safety of Decommissioned NPP Site Contamination and Deregulation> ordered by Korea Hydro & Nuclear Power (KHNP): ▲groundwater monitoring and contamination assessment technology for decommissioned NPPs, ▲radioactive contaminated soil/groundwater restoration technology, ▲site deregulation/safety assessment technology, and ▲site reuse assessment technology. In October last year, Hyundai E&C further developed technology for restoration of NPP decommissioning sites (technology for reducing wastes of radioactive cesium contaminated soil using particle size classification and cation exchange cleaning process), which received green certification from the Ministry of Environment. Hyundai E&C is the first and only company to receive green certification in the field of radioactive contaminated soil restoration.
“As a NPP expert, I participated in the green certification process for radioactive contaminated soil restoration technology. Under the presence of KHNP, we built a Pilot Plant* to evaluate the technology's performance and found that 90% of cesium was removed radioactively contaminated soil weighing more than 900 kg per hour.”
*Pilot Plant: A plant built for pilot testing (to check how the full system performs before commercializing the technology).
[ Site restoration is the process of returning the land to its natural state prior to the construction of a NPP. Contaminated soil and groundwater must be restored to truly complete decommissioning. ]
Hyundai E&C is working hard to secure source technologies in order to gain an advantageous position in the global nuclear decommissioning market. “Performing nuclear decommissioning without a track record of large-scale NPP construction is like trying to find your way without a map,” said Oh Seung-joon emphasizing the company's competitiveness.
“Hyundai E&C's strength is its excellent manpower and technology. We have all the data needed to build a large NPP, including drawings, construction procedures, design changes, various inspection documents and technical reports. The dismantling of the structure is carried out in the reverse order of construction. With our unrivaled know-how, we expect to make a significant difference in the field of nuclear decommissioning."
First Korean company to work on a nuclear decommissioning PM project in the U.S.
Hyundai E&C has fully initiated a NPP decommissioning business, starting with a contract for the ‘Decommissioned Site Contamination and Deregulation Safety Assessment’ for the Kori 1 NPP ordered by KHNP. Last year, it became the first Korean company to enter the U.S. nuclear decommissioning business. In March, Hyundai E&C signed a teaming agreement with Holtec to provide project management (PM) services for the Indian Point Energy Center (IPEC) NPP decommissioning project.
IPEC is a NPP in New York, U.S., consisting of three units (2317 MW). In April 2021, Unit 3 was the last of the three to permanently shut down, followed by the final transfer of ownership to Holtec in May of that year. Through the cooperation agreement, the two companies agreed on a number of areas including ▶Hyundai E&C’s direct participation in the decommissioning project of the Holtec-owned NPP in the U.S., ▶ joint entry into the global nuclear decommissioning market, and ▶joint marketing and bidding activities.
[ Hyundai E&C signed a nuclear decommissioning cooperation agreement, including a PM contract, with Holtec's Indian Point NPP in New York State in March last year. Photo includes Hyundai E&C CEO Yoon Young-joon (left) and Holtec CEO & President Kris Singh. ]
Last September, Hyundai E&C's nuclear experts boarded a flight to the U.S. to work on the Indian Point NPP Decommissioning Project. All of them are veterans with more than 10 years of experience in the nuclear field, and they will perform the following tasks at the IPEC site: ▶cutting and dismantling the reactor and other main components, ▶metal waste disposal and site restoration, ▶and project management for the dry storage facility for spent nuclear fuel. As their Korean control tower, until their departure, Oh Seung-joon provided step-by-step training on nuclear decommissioning and organized tours of the decommissioning facilities to ensure that these experts were ready to take up their roles once they begin working on the site.
“Hyundai E&C has made a lot of preparations for nuclear decommissioning, and joining the IPEC project is part of our journey to become a 'nuclear decommissioning leader'. I was in charge of managing the project at the headquarters level by closely communicating with the dispatched employees, as well as integrated handling of all data and technology acquired at the IPEC site. I take great pride in being able to help strengthen our company's portfolio.”
[ Hyundai E&C's nuclear experts working on the Indian Point nuclear decommissioning project. ]
Hyundai E&C is involved in all aspects of the Indian Point NPP decommissioning project, including decommissioning process and construction planning, large equipment volume reduction*, chemical decontamination, cutting of reactor pressure vessels and internal components, and dry storage of spent nuclear fuel (cask storage and transportation). As Hyundai E&C is the only builder in Korea that directly performs PM services for nuclear decommissioning, our employees at the U.S. nuclear decommissioning site are also working with great enthusiasm.
*Volume reduction: reducing the volume of waste by shredding, dehydrating, drying, incinerating, etc.
"I had a hard time adjusting to the time difference, culture, etc. in the beginning. On top of that, there was a lot of pressure to make a good impression of our company with our performance. I still have a lot on my shoulders, but I've adjusted and we're all getting along well. We are working hard to show off K-NPP technology (laughs)."
Decommissioning nuclear site with daddy’s heart, so two daughters can play in
Oh Seung-joon has been working in nuclear power for about 17 years. He has visited various NPP sites and participated in various projects related to nuclear power generation, but there are still many things he wants to do. He would also like to work on small module reactors and nuclear decommissioning site orders that our company will win in the future.
“If Hyundai E&C is awarded the project to decommission the Kori 1 NPP, I would like to work on the site from the start. I have a lot of affection for Kori 1 because I worked on the site of Kori 1-4, and I would like to apply the technologies developed by our company to the site. By the time I retire, I hope to have experienced all areas of nuclear power generation, from the construction of large NPPs and small modular nuclear reactors to nuclear decommissioning and spent fuel storage facilities.”
Outside of work, Oh is a husband to his lovely wife and a father to two daughters, ages 10 and 7. “Explaining the A to Z of NPPs to my family has made them all semi-experts,” he smiles.
“Even my family is now talking about the safety of nuclear energy (laughs). Nuclear energy is really safe engineering. NPPs are safe energy facilities, and we are doing everything we can to make sure that our children will be safe to play in nuclear decommissioning sites in the future, so stay tuned!”