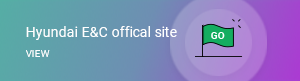
Off-Site construction shifts the paradigm of construction
Materials and equipment are stacked high on a construction site. Workers are rushing to and from the site, machining and fabricating installations. This is what we typically think of when it comes to construction sites, but that is now changing. Pre-fabricated building materials are assembled like Lego blocks, with no loud construction noise or dust to be found.
This is what off-site construction (OSC) has done to construction sites. OSC, which is gaining traction in recent years, is driving a shift from traditional on-site production to factory-based production. It is thus known as a revolution in the method of construction. This is a smart construction technology that can solve many of the problems facing the construction industry while increasing productivity and being environmentally friendly. Indeed, the era of OSC has begun.
What is OSC(Off-Site Construction)?
OSC is a construction method in which building structures, components, parts, and equipment are pre-fabricated in a factory and then transported to the construction site for assembly and installation. In simple terms, it is a method of pre-fabricating structures off-site and minimizing work on-site. In the field of architecture, it is mainly used for buildings with a simple and reproducible structure and form, such as hospitals, hotels, and schools, and in civil engineering, it is used for the construction of various structures.
In fact, the concept of OSC is not new. Precast concrete (PC), the dominant form of OSC construction method, first appeared in Korea in 1960 and drew interest in the early 1990s. At that time, Korea's construction sector was not actively developing due to lack of construction technology and the housing downturn caused by the Asian financial crisis, but it began to boom again in the mid-2000s. The reason why OSC has recently gained more traction is because it is regarded as an alternative to address problems such as the shortage of construction labor and the aging of skilled workers, and to enhance the safety and quality of workers.
Off-site Construction) vs. On-site Construction
What are the main differences between off-site OSC and on-site construction? First of all, the process is simple, and the construction period can be shortened because the structure is fabricated separately in the factory at the same time as the foundation. According to the Ministry of Land, Infrastructure, and Transport, the modular construction method, which is part of OSC, can cut construction time by 50% compared to the conventional method of reinforced concrete construction, which involves assembling rebar and placing concrete.
It is also effective for increasing production efficiency by standardizing and componentizing building structures. It is also less affected by external factors such as weather and climate, so it ensures stable manufacturing. Another advantage of OSC is that it not only reduces waste generation by standardizing materials in advance and fabricating only as much as needed, but also enables a low-carbon construction system by reducing noise, dust, and greenhouse gases that can be emitted during operations.
Types of OSC: PC Method vs. Modular Method
OSC is divided into “PC (Precast Concrete) method” and “Modular construction method” based on how the structural elements of OSC are stacked.
First, the PC method involves the manufacturing of major concrete components such as columns, beams, walls, and slabs in a factory and installing them on site. Unlike a typical construction site, where temporary molds are built, the concrete is poured, cured, and then used, the PC method involves pre-fabricating them in a factory and then assembling them on site like Lego blocks.
The PC method was mainly used for underground structures, such as parking lots under apartments. Recently, it has been applied to ground structures such as semiconductor factories and data centers, with expanded applications. In addition, the PC method that can apply to the construction of bridges and breakwaters has been developed, with diverse applications in civil engineering works.
The PC method is further categorized according to the type of structure. In particular, for residential buildings, depending on the structure, the wall supporting the ceiling instead of the column is called a wall structure, and the structure in which the 'columns' supporting vertical forces and 'beams' that support horizontal forces preserve the load is called a Rahmen structure.
Typical apartments are mainly built with a wall structure, but in recent years, there have been an increasing number of attempts to apply the PC Rahmen structure* to apartments with high space utilization. The Rahmen structure supports the load with columns and beams rather than walls, so it is easy to adjust the interior space to suit the user's needs, and it creates a sense of openness that makes the room appear spacious. In particular, noise from the upper and lower floors is not transmitted through the walls, and the beams between floors act as a buffer to reduce inter-floor noise. For this reason, Hyundai E&C is also applying the PC Rahmen structure - easily adaptable to different spaces- to "H Silent Lab", a research facility specialized in inter-floor noise, and is conducting relevant studies.
*PC Rahmen structure: A Rahmen structure that is assembled on-site using the PC method.
By contrast, modular construction can be further divided into steel modules and concrete modules, depending on the materials used. As the name suggests, "modular" construction involves the pre-fabrication of standardized, three-dimensional interior spaces in a factory. Modular method involves fabricating about 50 to 80 % of the entire process in a factory and then transporting the modules to the construction site to complete the construction with only simple assembly.
In particular, the Modular method is gaining traction as an ecological method compared to the conventional method of construction because it is simple enough to complete construction through “pre-fabrication” and “on-site assembly”. Not only does it reduce carbon emissions from construction sites, but it also has a high recycling rate, as used mobile modular homes can be dismantled and repaired at the factory and reinstalled where needed. Additional advantages include reduction in the cost of handling construction waste and the amount of energy used.
How far has OSC progressed abroad?
In Europe, North America, and other parts of the world, OSC has been actively implemented for the past 20 to 30 years. One of the reasons is the high cost of labor. In European countries, the share of OSC is around 20-25% of the total construction market, with the Nordic countries in particular having a share of over 40%.
In Asia, Japan introduced the modular method as early as the 1950s and 1960s, and since 2010, the demand for modular construction has increased significantly, especially for social housing. Today, about 120,000 to 150,000 modular homes are built annually, accounting for about 15% of the total housing market. China is also a latecomer to the OSC scene, pushing ahead with industrialized housing. In 2015, China completed a 57-story building in Hunan province in just 19 days, and during the COVID-19 outbreak, the country completed two hospitals in Wuhan city with 1000 and 1300 beds, respectively, in just 10 days.
Then, how big is the global modular construction market? According to global market analysts, “Market and Market”, the global modular construction market is expected to exceed approximately $108.8 billion by 2025.
Hyundai E&C, a leader in OCS
OSC is also gaining prominence in Korea as one of the future building technologies. The Ministry of Land, Infrastructure, and Transport announced the "Smart Construction Revitalization Plan" and is preparing a strategy to promote OSC by ordering the construction of OSC-based public housing in the number of 1,000 units by 2023 and providing benefits to ease floor area ratio, floor area ratio, and height restrictions at the permit stage.
Hyundai E&C, which is leading the way toward the smarter construction industry, is already reviewing the direction of future construction technology by establishing a TFT on OSC in 2020 while striving to develop technologies in specific areas. If the conventional OSC has focused solely on the construction sector, Hyundai E&C is expanding its applications to civil engineering such as bridges and breakwaters.
In particular, as for the Sheikh Jaber Causeway, a maritime bridge built by Hyundai E&C in Kuwait, the PC method was applied, where pre-fabricated box girders for the bridge deck were pre-fabricated in a factory and transported to the site for installation. The entire process of fabrication, transportation, and installation was completed through automated construction process, which not only shortened the construction time but also reduced costs. Hyundai E&C used the Full Span Launching Method (FSLM)* to install the world's largest box girder, which is 60 meters long, 4 meters high, and weighs 1,700 tons, offshore.
*FSLM method: A method in which pre-fabricated bridge decks of one span (distance between piers) are brought to sea and constructed in batches.
The architectural arena has already been experimenting with OSC since 2015, applying the PC method to the exterior walls of underground parking lots. In 2021, Hyundai E&C developed the “End Reinforced PC Double Wall Composite Method”, creating a big buzz in the construction industry. The PC double wall method involves pre-fabricating the two PC (Pre Cast) wall plates and then connecting them on site to form an integrated single wall. Compared to the conventional method, it shortens the construction period by about 30% and reduces safety accidents on site by simplifying the process. In addition, by strengthening the durability of the wall, Hyundai E&C has ensured greater seismic resistance as well as quality against leakage.
The PC double wall method has been designated as a new construction technology (No. 920) by the Ministry of Land, Infrastructure, and Transport, and four related patents have been registered. This demonstrates the progressiveness and field applicability of the technology. In particular, the PC double wall method is considered an essential method for future smart construction as it is performed in an automated production plant based on BIM.
In addition, for bridge construction, Hyundai E&C developed and patented a pre-fabricated pier system that extends the application of the PC method, which was only applicable to the superstructure, to the substructure including Pier-Cap* and columns. The pre-fabrication of Pier-Cap and columns at the factory not only enhanced durability and efficient quality control, but also shortened the construction period as it could be carried out at the same time as the foundation plate construction on site.
*Pier-Cap: A structure installed on top of a column to support the superstructure.
Breakwater construction also adopted OSC. Due to the nature of breakwater wall construction placing concrete at sea, seawater often interrupted operations. Therefore, Hyundai E&C applied the PC method, in which the outer wall of the superstructure of the breakwater is made of PC blocks and mounted, achieving a 30% reduction in construction time compared to conventional breakwater construction.
Off-site construction, OSC, has emerged as a new wave in the construction sector! OSC, which minimizes on-site work in the existing site-oriented construction sector, is an irreversible paradigm shift and an indispensable approach for future smart construction. Hyundai E&C, keeping up with the changing trends and leading the future of construction, plans to create a better construction environment by developing and introducing OSC technology based on smart technologies of the industry 4.0, including advanced robots and AI.