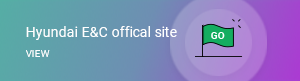
[ The entrance to Boryeong Undersea Tunnel, completed by Hyundai E&C in December 2021 ]
Recently, Boryeong Undersea Tunnel, which connects Sinheuk-dong, Boryeong-si, Chungcheongnam-do, to Wonsando-ri, Ocheon-myeon, was opened. National Route 77, which had been cut off by the West Sea, is finally connected. Boryeong Undersea Tunnel is the longest undersea tunnel in Korea and the fifth longest in the world. 11 years after breaking ground, Hyundai E&C completed Boryeong Undersea Tunnel using the “New Australian Tunneling Method (NATM)’, which involves detonating explosives and tunneling advancing forward and the “Waterproof Grouting Method” effective for preventing inflow of seawater. Let us have a look into the two state-of-the art construction methods of Hyundai E&C which culminated into Boryeong Undersea Tunnel after its struggle with seawater for some4,000 days, and also the benefits the tunnel opening will bring about.
Boryeong Undersea Tunnel, a Sea Route Connecting Boryeong and Taean
Boryeong Undersea Tunnel, which opened in December last year, is a four-lane road that runs through the sea floor from the ascending lane Taean to the descending lane Boryeong. It is a part of the road construction work between Boreyong and Taean, connecting Sinheuk-dong, Boryeong-si to Gonam-ri, Gonam-myeon, Taean-gun. The project for Boryeong Undersea Tunnel was first planned in 1998 to connect National Road 77, which was cut off by the West Sea, and later took shape through a preliminary feasibility study and basic design phase.
In fact, according to the basic design, tunnel was only 2,400 meters long. Initially, the section consisted of a bridge, an artificial island, undersea tunnel, and road. It was not about building a 7,000 meter long undersea tunnel. From the bridge that begins at the Daecheon Intersection, an artificial island connecting the undersea tunnel and the bridge was supposed to be built. However, Hyundai E&C changed its design to make the entire section into an undersea tunnel due to lack of commercial and environmental viability.
Boryeong Undersea Tunnel, which began construction in December 2010, was finally in service in December 2021, 11 years after breaking ground. Both the ascending and descending lanes were traversed in 2019, followed by finishing works such as draining pipe installation and road pavement. This made it possible for citizens of Taean and Boryeong, who had to make detours through other regions, to travel directly and tourists to travel more conveniently.
NATM Tunneling Method Applied to Boryeong Undersea Tunnel
Then, how was it possible to make a road for cars to run through the ocean floor? The undersea tunnelling method, which was frequently used in the early days, is a “cut and cover method”. It involves building temporary dams on both sides of the tunnel, pumping out stagnant water, digging the floor again to create a tunnel, then covering it, and demolishing the dams. The disadvantage is that it costs a lot of manpower, equipment, and money because a dam has to be created artificially to pump water out and put it back in. Another method, the “immersion method”, is to build tunnels on land in advance for each section and then assemble them under the sea. Both ends of the tunnel are blocked and the seawater inflow in the joint section is completely blocked, so this method is mainly used in places with weak ground.
However, Hyundai E&C used the “NATM method” instead of the cut-and-cover method or immersion method for building Boryeong Undersea Tunnel. The NATM method involves detonating explosives to dig through the rock while advancing forward, spraying concrete on the rock wall, and reinforcing it with iron everywhere. It allows construction while using the existing ground as a support, enabling fast tunneling speed, high durability, and wide range of applicable cross-sections, resulting in outstanding construction and economic performance. Therefore it is often used not only for the seabed but also for ground tunnel construction. Boryeong Undersea Tunnel is the first in Korea to apply the NATM method to undersea sections.
However, in the case of undersea tunnel construction, it is difficult to determine in advance which bedrock is weak because there are limitations regarding the preliminary geological survey. Furthermore, unlike general ground tunnels, there is another risk of seawater inflow along with a potential risk of collapse. If a large amount of seawater is accidentally introduced, it is not only challenging to ensure the safety of field workers, but also the stability and construction of the tunnel are undermined, and permanent seawater treatment costs become excessive during the actual operation.
However, the NATM method can flexibly cope with ground deformation, enabling the most prompt response. In addition, the works are driven by machines, so construction is possible with only a small number of people, curved tunnels can be built, and digging is done inside the ground, thereby minimizing impact on the surrounding environment such as mountains and waters. Hyundai E&C carried out the project while protecting not only the surrounding natural environment but also the livelihood of fishermen, as Boryeong Undersea Tunnel is located at the entrance of Cheonsu Bay. In other words, the NATM method is indeed the most optimal and best option considering the special environment of the seabed.
Blasting NATM Method for Seabed Section: Higher Stability, Durability and Environmental Protection
Let's take a look at the construction procedures using the NATM method, the core of building Boryeong Undersea Tunnel. First, the bedrock in the direction in which the road should be made is accurately analyzed, and the blasting position is determined according to the result. Accordingly, holes for explosive installation are drilled, and Hyundai E&C has improved accuracy by using advanced drilling machine that can control the location and depth of the holes with computers. Afterwards, explosive is placed in the hole drilled according to the standard, blasting operation is conducted according to safety requirements, and ground is dug while advancing forward, meeting the tunnel shape. The blasting rocks generated at this time are taken out of the construction site using large equipment.
If the previous step is safely completed, then now is time to increase the stability of the ground. First, concrete is sprayed onto the construction surface with compressed air to reinforce the ground weakened by blasting. After that, rock-bolt as well as a structure supporting the ground are also installed to suture the reinforced ground with the solid ground of the existing rock. Rock-bolt is a rebar that is inserted vertically into the cross section of the tunnel, and Boryeong Undersea Tunnel used CT-rock-bolt, which is effective against salt water corrosion. The concrete is spewed for the second time to make the tunnel harder. This series of processes is called the primary support phase.
After the primary support stage of the NATM, long-term stability is secured through concrete lining, the secondary support stage. A waterproof film is installed on the excavation surface where the first supporting material is applied to prevent groundwater from flowing in. Subsequently, utility-pipe conduit is placed for installation of electricity, communication lines, and drainage pipes, supporting reinforcement for lining is assembled, and then concrete is applied to improve the durability of the tunnel. This secondary support stage helps to protect the tunnel's internal facilities and maintain pleasant interior space, finally allowing the tunnel to take the shape of the road-type tunnel that is often seen when driving on general roads.
[ Part of Boryeong Undersea Tunnel is equipped with special lighting and tile art expressing the sea to create an atmosphere as if walking in the deep sea ]
Waterproof Grouting Method: 24/7 War against Seawater
If we have to prepare for a collapse during a tunnel construction on the ground, one more thing is needed for an undersea tunnel: war against water. To this end, Hyundai E&C considered the environmental specificity of underwater throughout entire project from design to construction. This is also why the “waterproof grouting method” was used together with NATM. It is to ensure maximum safety by controlling seawater that may flow in during blasting. Waterproof grouting is a method of maximizing tunnel stability by preventing seawater from entering the tunnel and strengthening the durability of the crush zones (the broken rock along the fault) and the bedrock. The amount of seawater and groundwater entering the tunnel during tunneling of the undersea section is checked, and when the inflow exceeds the requirement level, waterproof materials(cement liquid preventing water inflow) with minimum 17 (number of holes) to maximum 68 are injected into the bedrock to block seawater inflow.
Since the NATM method mainly blasts using explosives, there is a high possibility that the ground will collapse and a large amount of seawater will flow in the soft rock and crush zones. To prevent this, Hyundai E&C conducted an accurate three-step geological analysis using 3D computing prior to digging. The first step is “Tunnel Seism Prediction (TSP) exploration” which can even identify the characteristics of the 200m ground ahead. When an elastic wave is transmitted to the ground by creating an impact at one point, the wave encounters another medium in progress, and some of it is refracted and reflected. This characteristic was applied to geological exploration, and the concept of exploration for oil drilling was applied to the tunnel, which helps to determine the geological state ahead.
The second step is ‘advanced horizontal drilling” to check the geological and rock conditions 60m ahead. Since the sample is directly extracted, the ground state can be accurately identified than the TSP method. When sudden elution occurs during drilling, a device to prevent it at high pressure is installed to check the water pressure and flow rate at 3-m intervals, and if necessary, a water pressure test is conducted. The final third step is using a “probe hole” that punctures the last 20m, basically drilling three holes to determine whether to implement waterproof grouting by identifying the actual rock quality and inflow around the tunnel. Waterproof grouting is immediately performed when seawater is 4L or more/minute/hole of probe hole, or 8L or more/minute is eluted in total of 3 holes of probe hole.
As such, accurate geological survey is conducted over three steps, and waterproof grouting is determined according to the results. Considering the ground flow and inflow quantity according to the geological survey results, the injection pressure of the waterproof material that prevents seawater inflow is determined, and depending on the type, a long hole of 18 to 20m is drilled in front of the tunnel at 15~24 degrees to inject the waterproof material at high pressure. When the amount of gush-out water is large and the ground is unstable, it is very difficult to inject a constant pressure and a certain amount of waterproof materials with the existing grouting equipment. Therefore, Hyundai E&C used the “IMG Construction Method” to control waterproof materials more precisely.
The IMG method can be applied to all injection materials, the injection amount and can be checked in real-time during work, and injection at constant pressure through an automatic control system is possible. In addition, it consists of a large-volume pump and a multi-distribution system that can accommodate sufficient amounts even in high-pressure ground areas, thus demonstrating high constructability and economic viability. In addition, it is effective against reduced durability and environmental pollution because it does not use existing water glass (sodium silicate)-based injection materials. As such, Hyundai E&C progressed by an average of 3m per day by conducting reinforcement and waterproof work after drilling. Thanks to such efforts, there was not a single inflow of seawater at the Boryeong Undersea Tunnel construction site for 11 years from groundbreaking to completion.
Safety is No.1 Priority
Hyundai E&C has designed the tunnel to cope with various situations that may occur during construction by preparing step-by-step measures for dangerous sections. First of all, in case of passing through the poor geological section, the worked-on tunnel was divided into two sections. First, there was the preceding tunnel which first began drilling and the following tunnel at 200 m apart, and it was structured so that if an abnormality is found in front of the preceding tunnel, a follow-up measure was immediately carried out. If, according to the geological analysis, a crush zone or a poor geological zone was found in the front, a 1m thick waterproof door is installed in the preceding tunnel to prevent flooding. In the event of a collapse or flooding, the operator of the preceding tunnel is quickly pulled out, and the waterproof door is closed. As the preceding tunnel is flooded, the following tunnel at the rear of 200m moves forward while reinforcing it with waterproof grouting as much as possible, and then digging is done in the transverse direction where the preceding tunnel is located. After that, safety was secured by digging in the reverse direction towards the flooded tunnel to drain and penetrate the introduced water. As digging advanced forward, the waterproof door was dismantled, moved and re-installed.
In the above process, Hyundai E&C secured workers' safety through measures against various risks, such as completely blocking inflow of water and installing waterproof door, and as a result, Boryeong Undersea Tunnel was opened without a single safety-related accident. As a result, Hyundai E&C holds a leading position in the undersea tunnel construction, recognized for its construction expertise in the unknown field of subsea.
Connecting Disconnected National Route 77: Saving 80 Minutes in Travel
The benefits of Boryeong Undersea Tunnel are great. First of all, it is possible to go back and forth directly between Boryeong (Daecheon) and Taean. Previously, people had to travel about 75 kilometers for over 1.5 hours through Hongseong-gun and Seosan-si, Chungcheongnam-do, whereas now, after opening of Boryeong Undersea Tunnel, you only have to 15 kilometers, making it a 10 minute trip. In particular, the new tunnel is expected to facilitate logistics and transportation, allowing vehicles to travel in even in bad weather, promoting a balanced regional development and economic revitalization in nearby areas, and improving the living conditions of residents by providing infrastructures related with electricity, communications, and water supply.
In addition, in the past, National Route 77 from Busan Metropolitan City to Paju-si, Gyeonggi-do, was cut off by sea, limiting the development of the southwest region. However, Boryeong Undersea Tunnel is expected to play a role as a new tourism resource on the west coast by traversing the entrance of Cheonsuman Bay, a marine resource reserve, being connected to the Taean Coastal National Park, and bringing more vitality to local economy and the development of the entire region as well.
The construction of Boryeong Undersea Tunnel involved 50 equipment and about 200 people a day, which equals to 200,000 equipment and 800,000 people during the total construction period of about 4,000 days. It was indeed a national-scale construction project with a total budget of KRW 488.1 billion. Hyundai E&C used these resources, the NATM method, and waterproof grouting method to create a safe and durable tunnel. Why not travel 6,927m under the deep sea, through Boryeong Undersea Tunnel, which is a culmination of Hyundai E&C’s stable technology and the sweat and efforts of its employees. For your information, crossing Boryeong Undersea Tunnel is free of charge.